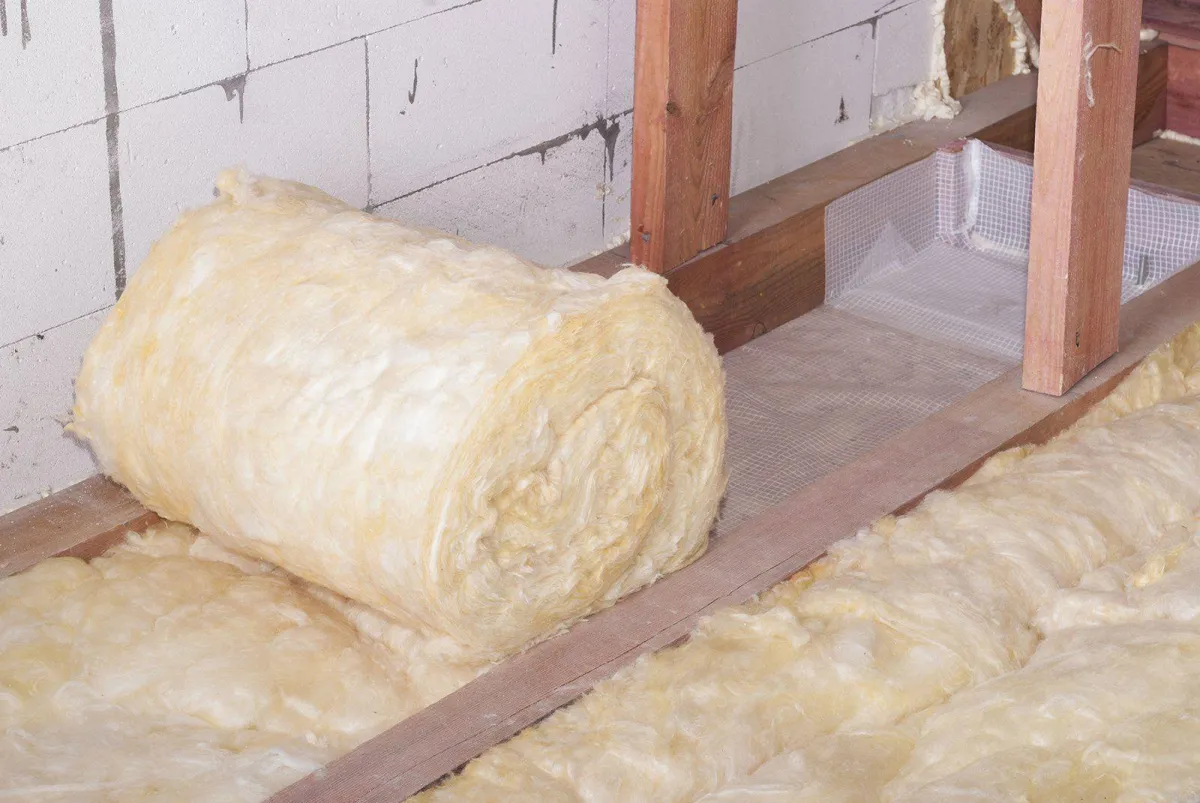
Spray Foam Insulation Removal: When & Why It's Necessary
Can Spray Foam Insulation Be Removed? When and Why You Might Need To
Homeowners often choose spray foam insulation for its excellent insulating properties and air-sealing capabilities. It creates a tight barrier that can significantly reduce energy bills and improve indoor comfort. But what happens when this seemingly perfect solution becomes a problem?
Yes, spray foam insulation can be removed, though the process is more complex and costly than removing traditional insulation types. Removal becomes necessary when facing installation problems, water damage, renovation needs, or code violations. Understanding when and why to remove spray foam can save you headaches and money in the long run.
Whether you're dealing with existing issues or planning future renovations, knowing your options for spray foam removal is key. This guide covers everything from identifying problems to finding the right professionals for the job, helping you make informed decisions about your home's insulation.
Understanding Spray Foam Insulation
Before diving into removal, it's helpful to understand what makes spray foam unique. Spray foam insulation comes in two main types: open-cell and closed-cell. Each has different properties that affect both performance and removal.
Types of Spray Foam Insulation
Open-cell foam is lighter, less dense, and more flexible. It offers good sound insulation but provides less thermal resistance per inch compared to closed-cell foam. Its softer nature makes it somewhat easier to remove.
Closed-cell foam is denser and more rigid, offering superior insulation values and adding structural strength to walls. This rigidity, while great for insulation performance, makes removal more challenging and often more expensive.
Benefits of Spray Foam Insulation
When properly installed, spray foam offers impressive benefits:
Superior R-value per inch (especially closed-cell)
Excellent air barrier properties
Moisture resistance (closed-cell)
Longevity (can last 20+ years)
Reduction in energy costs
These benefits explain why many homeowners choose spray foam, but they don't guarantee problem-free performance.
When Spray Foam Insulation Removal Becomes Necessary
Several situations might require removing spray foam insulation, each with its own challenges and considerations.
Poor Installation Issues
Poor installation is one of the most common reasons for removal. Signs of installation problems include:
Uneven application with gaps or thin spots
Off-ratio mixing leading to foam that never properly cures
Shrinkage that creates gaps over time
Strong odors that persist long after installation
Improper installation can negate many of spray foam's benefits and potentially create health hazards from chemical off-gassing.
Water Damage and Mold Growth
While closed-cell foam is water-resistant, installation problems can allow moisture to become trapped between the foam and building materials. This creates ideal conditions for mold and rot.
Signs of moisture problems include:
Discoloration of walls or ceilings
Musty odors
Visible mold growth
Soft or deteriorating building materials
Once moisture problems develop, removing the affected insulation is often the only effective solution.
Renovation or Remodeling Projects
Home renovations frequently require insulation removal, especially when:
Adding or relocating electrical wiring
Plumbing modifications are needed
Structural repairs must be made
Windows or doors are being repositioned
Unlike fiberglass batts that can be temporarily moved aside, spray foam adheres firmly to surfaces and must be cut out or completely removed.
Building Code Violations
Sometimes spray foam must be removed to address code violations:
Foam installed without required thermal barriers
Incorrect application in areas requiring fire-rated assemblies
Blocking of required ventilation spaces
Installation by unlicensed contractors (in some jurisdictions)
Building inspectors may require removal and replacement if these issues are discovered.
The Spray Foam Insulation Removal Process
Removing spray foam is significantly more labor-intensive than removing traditional insulation types.
DIY vs. Professional Removal
While DIY removal is possible for small areas, professional services are strongly recommended for larger jobs because:
Professionals have specialized tools designed specifically for foam removal
Safety equipment reduces exposure to dust and chemicals
Experience helps prevent damage to underlying structures
Proper disposal of removed materials follows local regulations
DIY removal often leads to increased damage and ultimately higher costs when professionals need to fix mistakes.
Removal Methods and Techniques
Professionals use several approaches depending on the situation:
Mechanical removal: Using specialized cutting tools, scrapers, and grinders to physically remove the foam
Chemical solvents: In some cases, specific solvents can help break down the foam's adhesion
Heat application: Warming the foam can sometimes make it easier to separate from surfaces
The best approach depends on the foam type, location, and what surfaces it's attached to.
Safety Considerations
Safety is paramount during spray foam removal due to:
Dust and particles that can irritate lungs and eyes
Potential chemical residue from uncured foam
Physical hazards from cutting and scraping tools
Confined spaces with limited ventilation
Professional removers use personal protective equipment including respirators, eye protection, and full-body coverings.
Costs of Spray Foam Insulation Removal
Removing spray foam insulation is significantly more expensive than removing traditional insulation types.
Factors Affecting Removal Costs
Several factors influence the final price:
Square footage of the area requiring removal
Accessibility of the insulation
Foam type (closed-cell is generally more difficult and expensive)
Attachment surfaces (foam on irregular surfaces takes longer to remove)
Local labor rates vary by region
Disposal fees which depend on local regulations
Average Cost Ranges
While costs vary widely based on the factors above:
Small jobs (under 100 square feet) typically range from $1-3 per square foot
Larger removal projects often run $2-5 per square foot
Whole-house removal can cost $15,000-30,000 or more
Additional repairs to surfaces after removal add to the total cost
These costs make prevention through proper initial installation extremely important.
Alternatives After Removal
Once spray foam has been removed, you'll need to choose a replacement insulation option.
Modern Insulation Options
Today's market offers several alternatives:
Mineral wool batts provide good fire resistance and sound dampening
Fiberglass batts offer affordable thermal performance
Cellulose provides an eco-friendly option with good thermal properties
Rigid foam boards offer high R-values without spray application
New spray foam applied correctly by reputable contractors
Each option has its own balance of cost, performance, and installation considerations.
Choosing the Right Replacement
When selecting new insulation, consider:
Climate zone requirements for R-value
Building design and special considerations
Budget constraints balancing immediate vs. long-term costs
Access issues that might favor certain installation types
Moisture management needs in your specific situation
Working with energy auditors or insulation specialists can help identify the best solution for your specific needs.
Preventing Future Insulation Problems
An ounce of prevention is worth a pound of cure, especially with spray foam insulation.
Proper Installation Practices
To avoid future removal needs:
Hire certified installers with specific experience in your insulation type
Check references and review previous work
Ensure proper preparation of surfaces before application
Verify ventilation requirements are understood and followed
Request detailed documentation of the installation process
Proper installation costs more initially but saves substantially in the long run.
Regular Inspection and Maintenance
Even with good installation, periodic checks help catch problems early:
Annual visual inspections for discoloration or changes
Checking for new gaps or separation from surfaces
Monitoring indoor air quality and unusual odors
Identifying and addressing small water leaks before they cause major damage
Early intervention can often prevent the need for complete removal.
Conclusion and Next Steps
Spray foam insulation removal, while challenging and expensive, sometimes becomes necessary to address problems or accommodate changes to your home. Understanding when removal is needed helps you make informed decisions and avoid larger issues down the road.
If you're facing potential spray foam problems, start with a professional assessment. An experienced contractor can evaluate whether removal is necessary or if other solutions might address your concerns.
For quality insulation services, whether installation, repair, or removal, contact Draft Busters Insulation. Their team of certified professionals can assess your situation and provide tailored solutions that ensure your home remains comfortable, energy-efficient, and problem-free for years to come. Don't let insulation issues compromise your home's performance – reach out to Draft Busters Insulation today for expert assistance with all your insulation needs.